Small Batch CNC Machining
With technological advancements, the uptake of small batch CNC machining has surged, resulting in efficient, precision-focused manufacturing and ensuring quick delivery of products that align with unique customer specifications.
What is Small Batch CNC Machining?
Small Batch CNC (Computer Numerical Control) Machining is a manufacturing process that creates precise parts in smaller quantities, typically ranging from one to several hundred units. It’s a popular choice for prototypes, custom orders, or small production runs where high precision is needed.
The process uses pre-programmed computer software to control the movement of machinery and tools. The computer controls can operate complex machinery such as grinders, mills, routers, and lathes, allowing for high accuracy and repeatability in manufacturing parts.
Small Batch CNC Machining contrasts with mass production that makes thousands or millions of identical parts. It provides a cost-effective solution for low-volume businesses needing high-quality, custom parts. The high customization, rapid prototyping, and reduced inventory costs make Small Batch CNC Machining an attractive option for many businesses.
Time Delivery Rate
Yield
Customer Satisfaction Rate
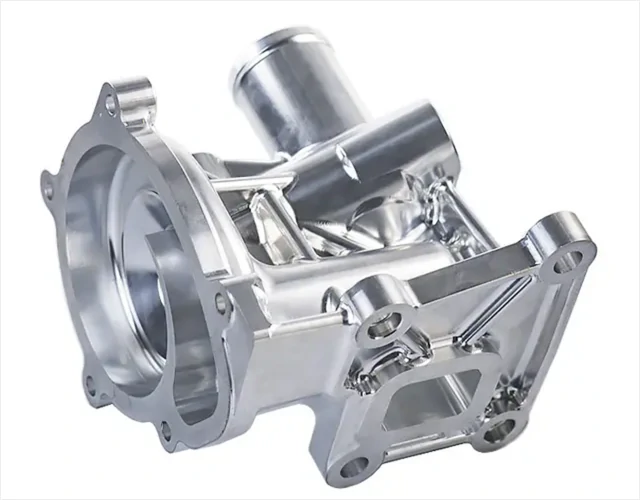
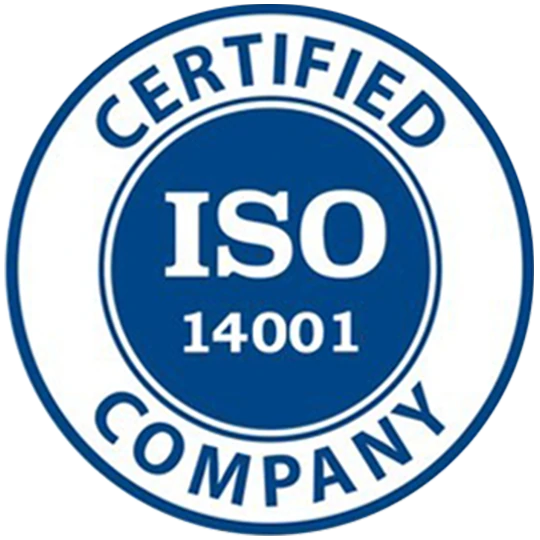
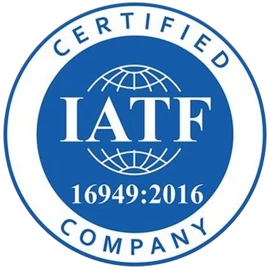
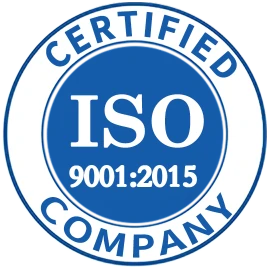
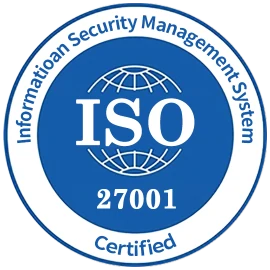
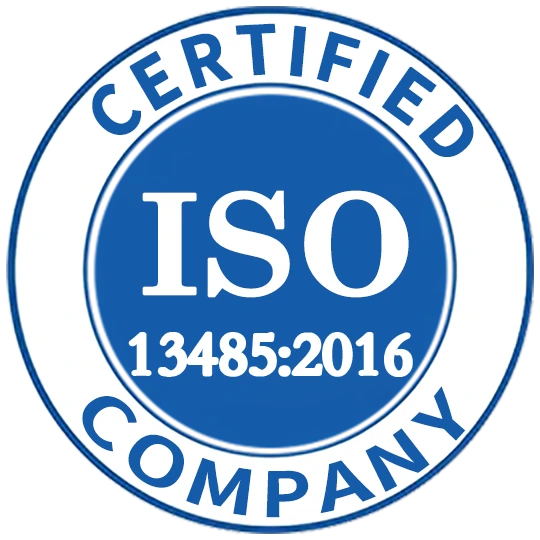
Advantages of Small Batch CNC Machining
Small batch CNC machining offers numerous advantages: greater flexibility, reduced inventory costs, easier customization, rapid prototyping, and superior precision. These benefits can lead to substantial cost savings and elevated customer satisfaction levels, making small batch CNC machining an attractive option for many businesses.

Greater Flexibility
Unlike mass production, small batch CNC machining allows manufacturers to quickly and efficiently adjust to changes in design or customer requirements. This agility can provide a significant competitive advantage in markets where customer needs, and trends evolve rapidly.

Reduced Inventory Costs
Small batch CNC machining allows manufacturers to produce only what’s needed, exactly when it’s required. This strategic, just-in-time approach minimizes storage costs for finished goods and raw materials, offering significant financial benefits.

Easier Customization
Since each batch is smaller, it’s easier to customize each product run to meet specific customer requirements. This is particularly advantageous in industries where tailored solutions are the norm, such as medical device manufacturing or aerospace engineering.

Superior Precision
CNC machining provides high precision and consistency. This is crucial for manufacturing high-quality parts. In small batch production, each piece can be monitored more closely for quality, ensuring that each part meets the stringent standards required.

Rapid Prototyping
Small batch CNC machining is perfect for creating prototypes. Businesses can test multiple designs, make quick adjustments, and then run a new batch of prototypes, facilitating faster product development cycles.

Cost-Effective for Low-Volume Production
For low-volume production, small batch CNC machining is more cost-effective than traditional methods. It saves on initial setup costs without requiring physical tooling like molds or dies. This makes small batch CNC a cost-efficient choice for small production runs.
Our Services
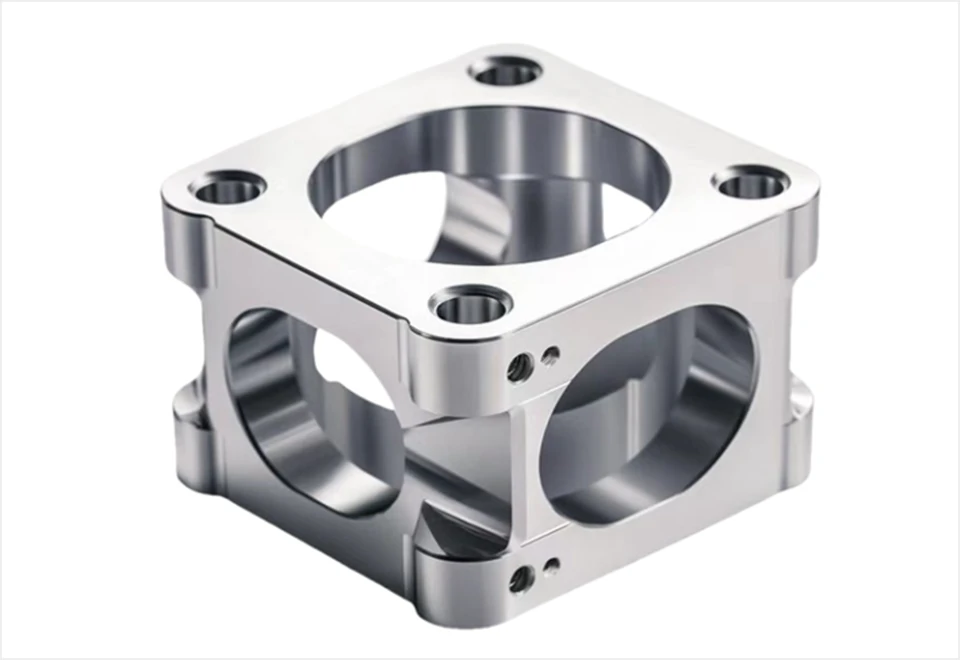
CNC Milling >
CNC milling manufactures complex geometric shapes and planes for a wide variety of products. Multi-axis metal CNC machine tools do not need to fix the mold, highly flexible, high precision. We have 3 axis, 4 axis, 5 axis machine, can meet the machining demand.
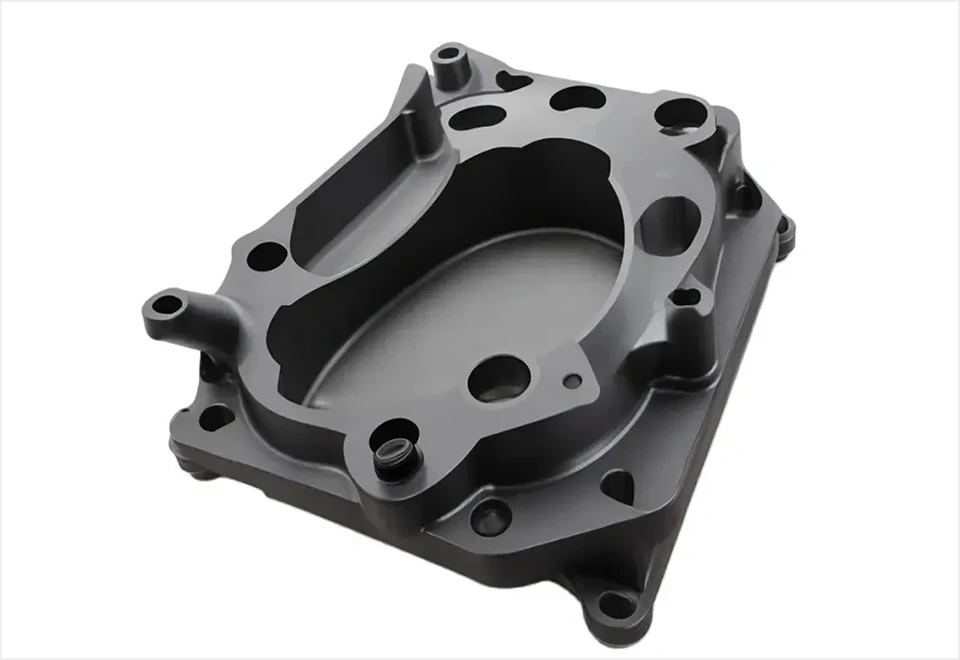
CNC Turning >
CNC Turning process to produce custom cylindrical shape prototypes and end-use production part. We use CNC lathes to machine features like axial and radial holes, flat openings, grooves.
CNC machining materials
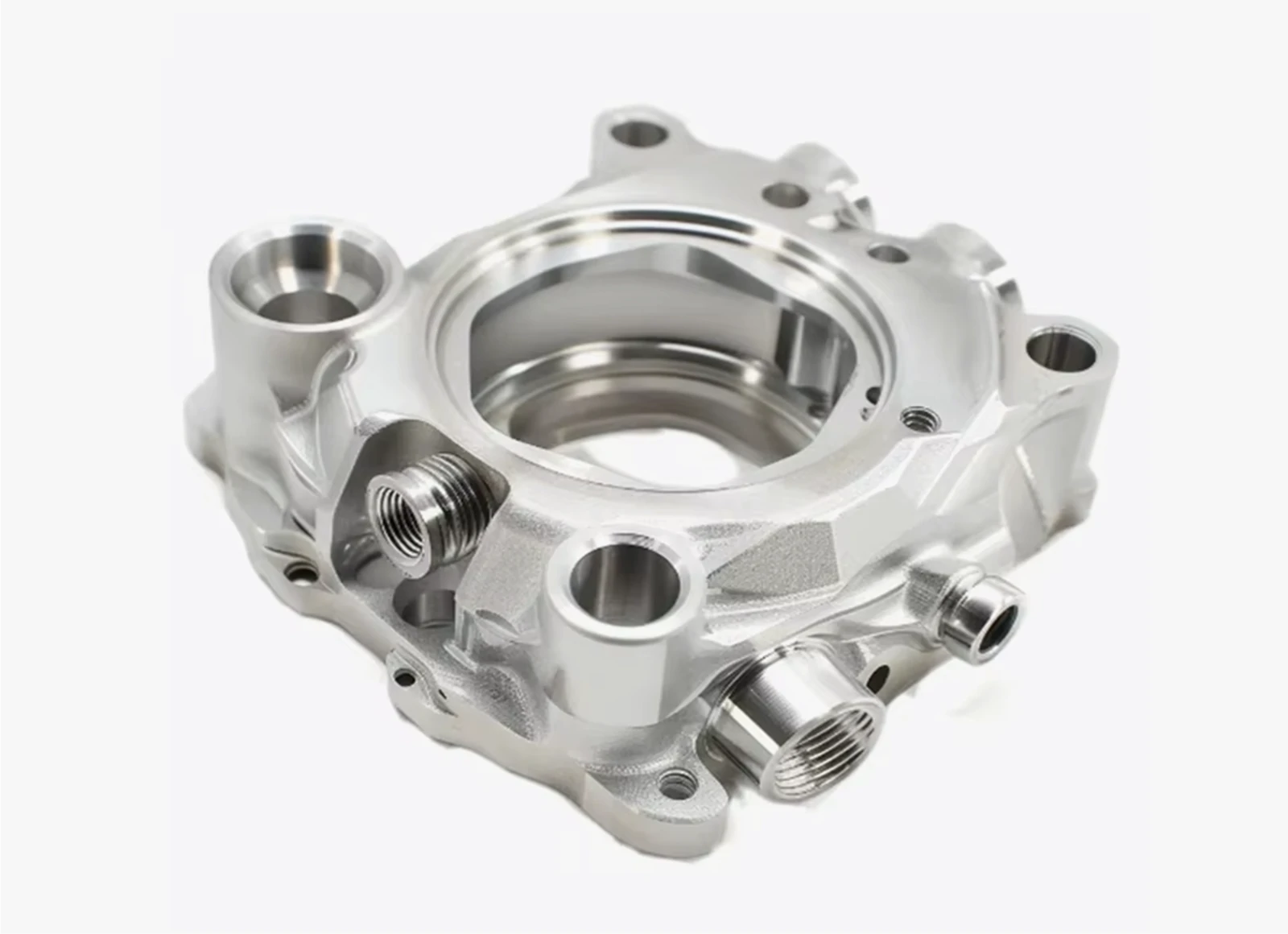
Aluminum
2024, 5052, 5083, 6063, 6061, 6082, 7050, 7075
Stainless Steel
17-4, 18-8, 303, 304, 316, 416, 420, 430, 410, 440C, 321, 347
Brass
C36000, C26000, C28000, C37700, C48500, C22000, C23000, C24000
Copper
C11000, C10100, C14500, C17200, C18200, C19400, C10200, C12200
Titanium
2024, 5052, 5083, 6063, 6061, 6082, 7050, 7075
Plastic
POM, ABS, Nylon, PEEK, PTFE, PAI, PMMA, PEI, HDPE, PVC, PPS, PC, UHMW
CNC machining surface finishes
Check The Characteristics of Materials to Choose the Best One for Your Project, Click “View All” to Learn More.
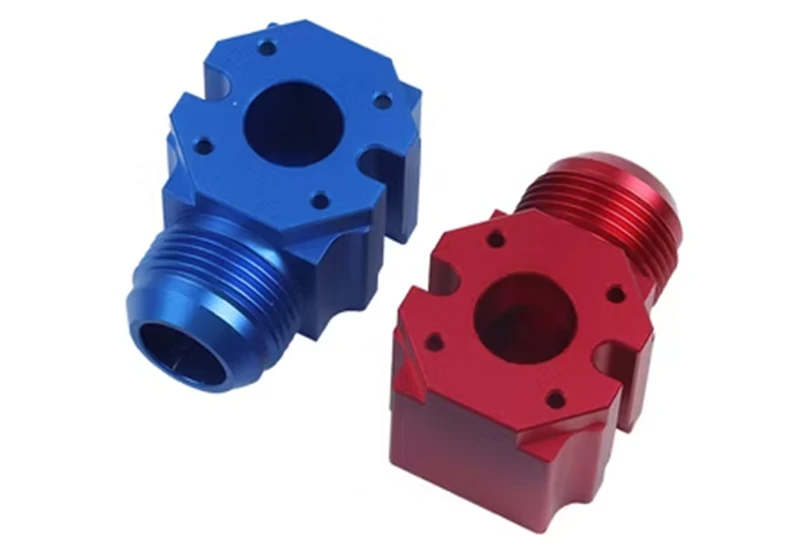
Painting
Applies a colored coating for aesthetics and protection.
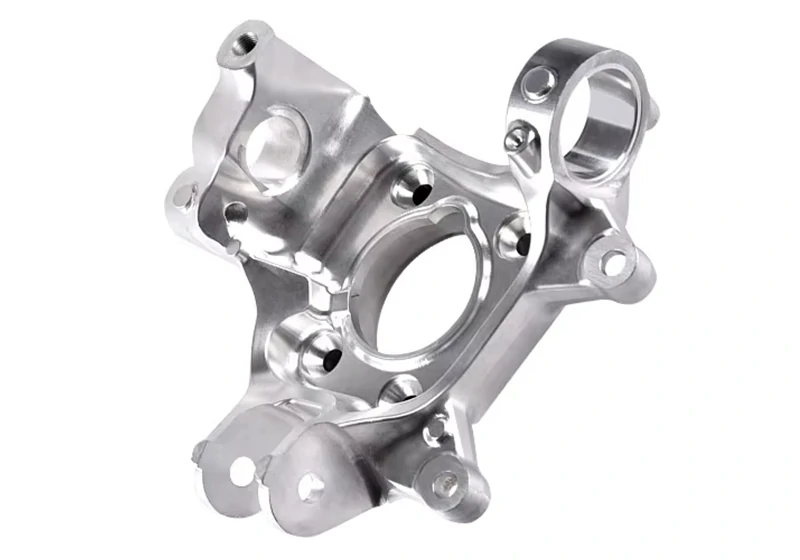
Passivation
Enhances corrosion resistance by removing free iron from surfaces.
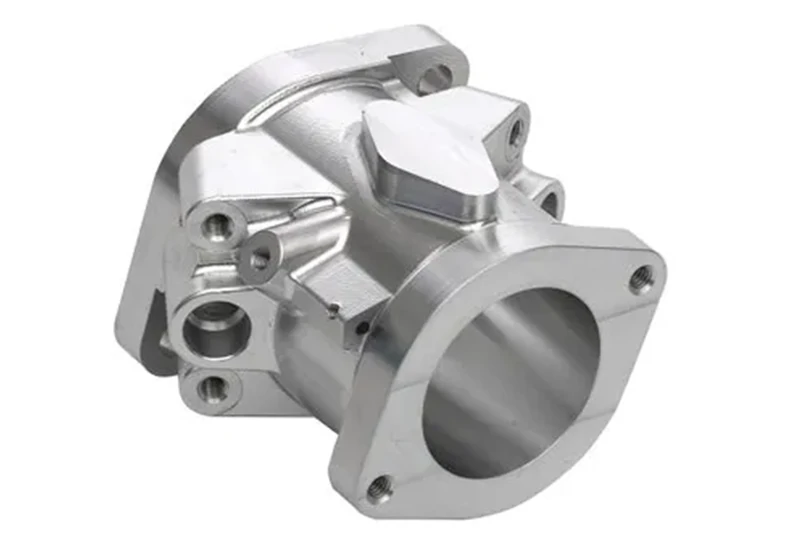
Powder Coating
Durable, powder-applied finish, baked to form a hard coat.
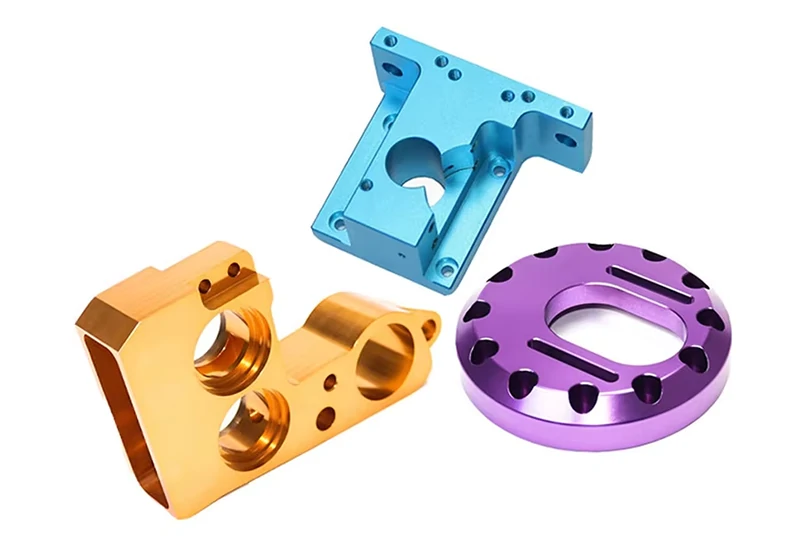
Anodizing
Electrochemical process creating a shiny or dull, corrosion-resistant layer.
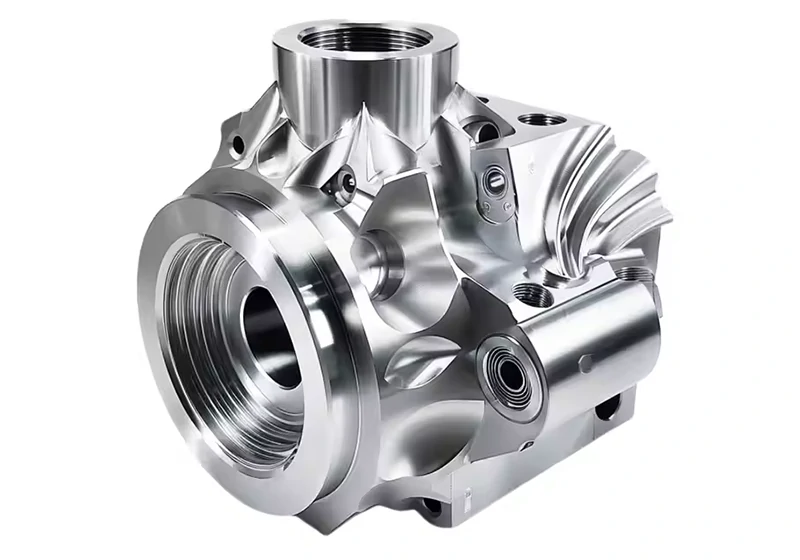
Polishing
Creates a smooth, shiny surface by mechanical abrasion or chemical treatment. (Ra 0.8μm / Ra 32μin or better)
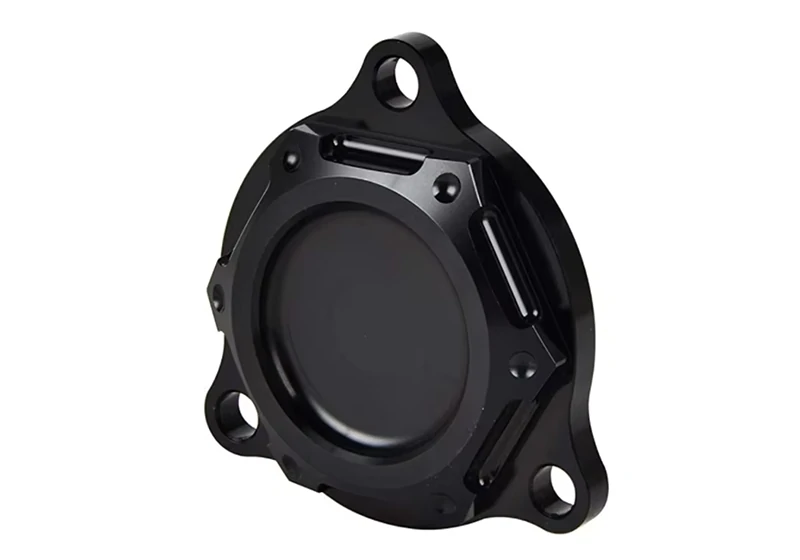
Black Oxide
Black conversion coating providing corrosion resistance.
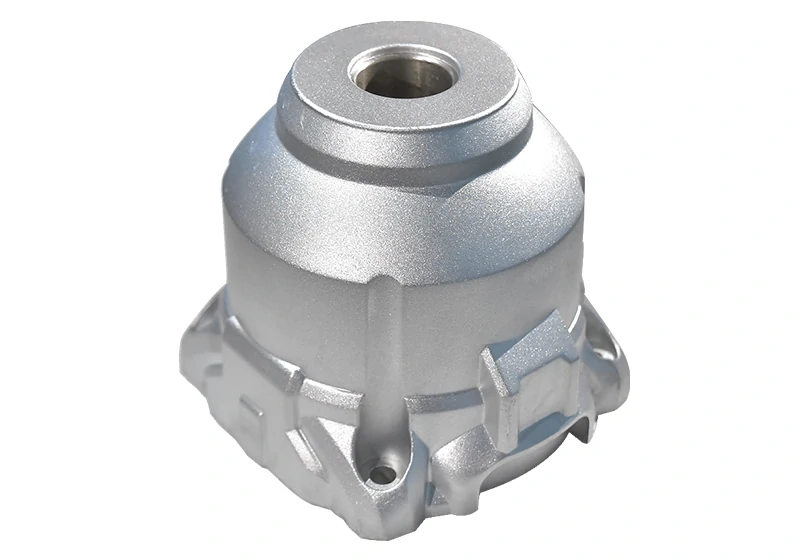
Sandblasting
Uses high-pressure sand to clean and texture surfaces, creating a matte finish.

Plating
Corrosion resistance, with solderability and electrical conductivity, various material options.
Specialist industries
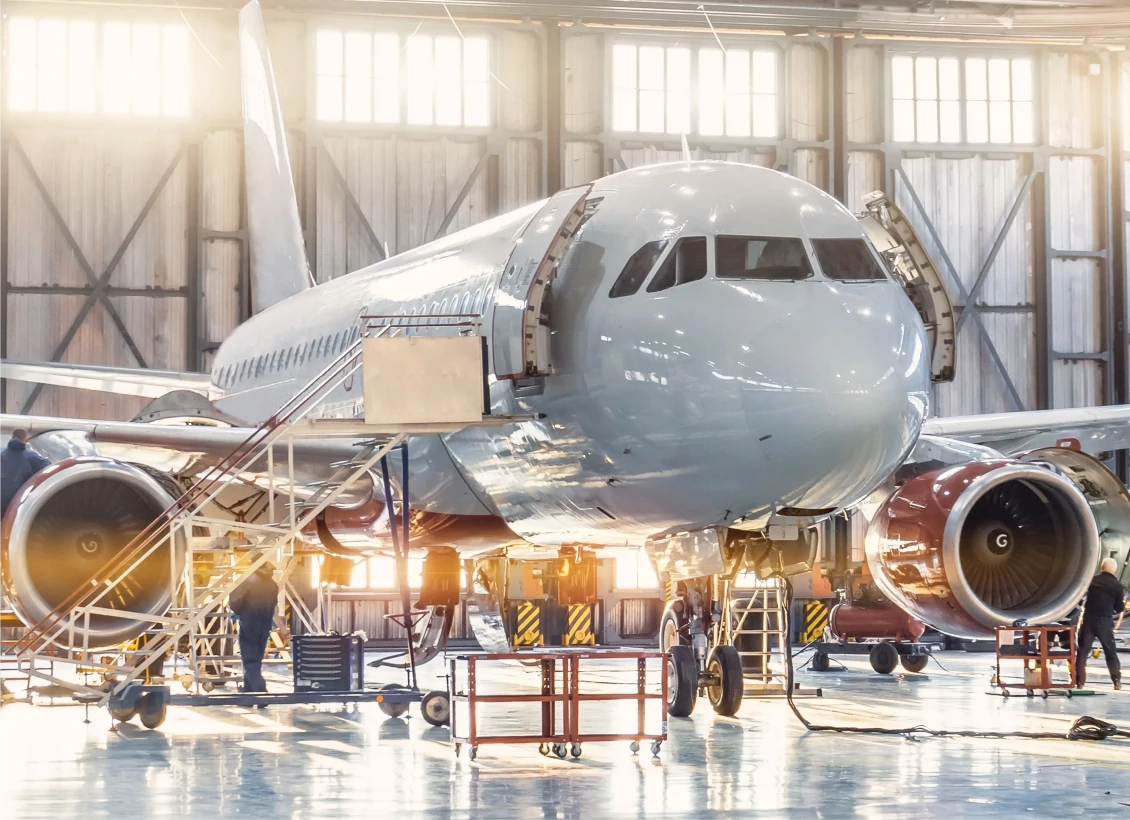
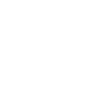
Aerospace & UAV

Automotive

Consumer Products

Industrial

Medical

Robotics
Request A Quote

Recent Articles/Blog
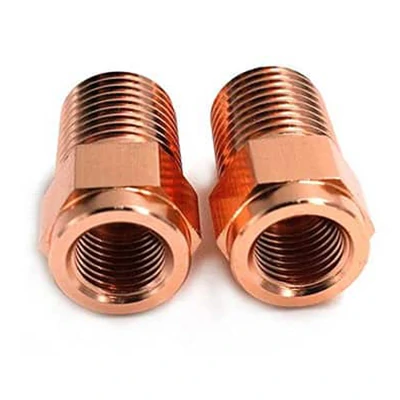
Metal Surface Finish: A Comprehensive Guide to Metal Finishing Processes
Metal surface finishing processes are treatments applied to metal surfaces to enhance appearance...
Read More →
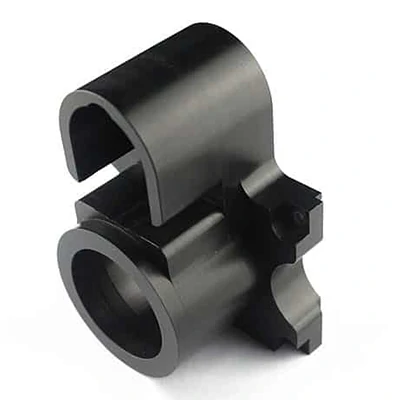
What is Slot Milling: Types, Techniques, Tips, and Advantages
Slot milling is a machining process where a milling cutter removes material from a workpiece to create slots...
Read More →
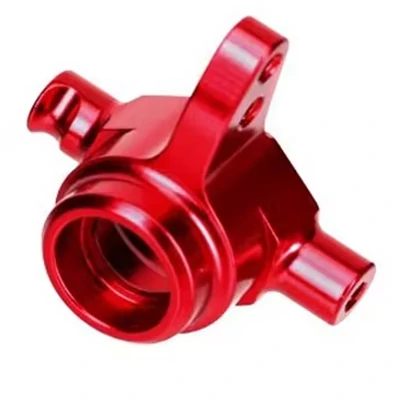
Precision CNC Milling Services
This manufacturing process works well for many materials, including metals, polymers, wood and glass....
Read More →
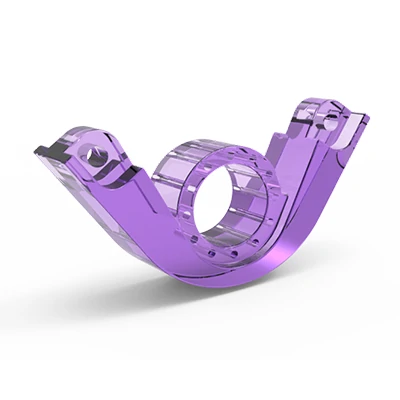
What is Slot Milling: Types, Techniques, Tips, and Advantages
Slot milling is a machining process where a milling cutter removes material from a workpiece to create slots...
Read More →